Why are four-row tapered roller bearings the first choice for industrial equipment upgrades? Luoyang INNO Bearing CO,LTD Revealing the four core advantages
Luoyang INNO Bearing CO,LTD professional analysis of the four major technical advantages of four-row tapered roller bearings under heavy load and high-speed conditions, providing customized bearing solutions, helping to increase equipment life by 30%+, click to get the bearing selection guide!
Industrial equipment upgrade, bearing performance determines production efficiency
In core areas such as metallurgy, mining, and heavy machinery, equipment has long faced severe challenges of high loads and strong impacts. Traditional double-row bearings are prone to early failure due to insufficient load capacity, and four-row tapered roller bearings are becoming a key breakthrough for equipment upgrades with their unique structural design and material technology.
Luoyang INNO Bearing CO,LTD Four differentiating advantages of four-row tapered roller bearings
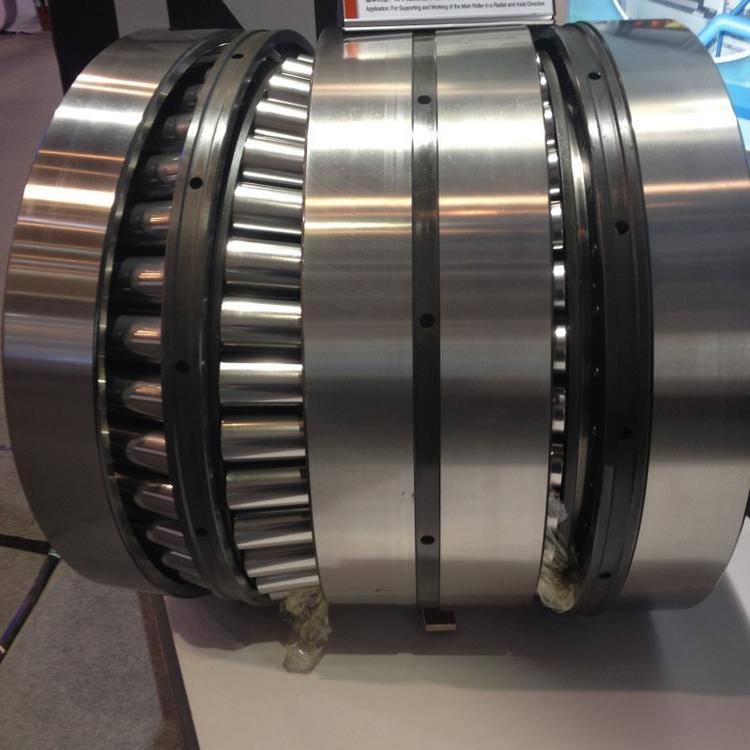
- Super strong load-bearing capacity, breaking the heavy load limit
- The four-row roller symmetrical arrangement structure is adopted, and the load distribution uniformity is improved by 40%
- The maximum radial load of a single set of bearings can reach 2000kN, and the axial load is 1200kN (supporting customized enhancement)
- Typical case: After the transformation of a rolling mill in a steel plant, the bearing life was extended from 6 months to 18 months
- Precision preload adjustment to ensure operational stability
- Exclusive tapered raceway grinding technology to ensure that the contact surface between the roller and the raceway reaches more than 98%
- Adjustable preload device to compensate for installation errors and reduce vibration values to ISO P5 standard
- Suitable for high-speed scenarios: The temperature rise is <35℃ when the measured linear speed reaches 45m/s
- Modular design doubles maintenance efficiency
- Split cage design supports single-row replacement and reduces maintenance costs by 60%
- Standard dust cover/seal ring (IP65 protection level) to adapt to harsh working conditions such as dust and high temperature
- Quick change case: The replacement time of a cement plant’s vertical mill bearing was shortened from 8 hours to 2.5 hours
- Full life cycle cost optimization plan
- Selected special steel + carburizing and quenching process, fatigue life reaches L10=50,000 hours
- Supports grease lubrication/oil mist lubrication dual mode, saving 15-25% of annual maintenance costs
- Provides bearing health monitoring system integration services, with a fault warning accuracy rate of ≥92%
Why choose Luoyang INNO Bearing CO,LTD ?
① 20 years of industry experience: Serving 300+ heavy industry customers worldwide, and delivering more than 500,000 sets of four-row tapered bearings
② Customized development capabilities:
Non-standard size customization (inner diameter φ50mm-φ2000mm)
Special working condition adaptation (high temperature resistance 400℃/corrosion resistance/vacuum environment)
③ One-stop service system:
Free bearing selection calculation software
48-hour emergency response mechanism
12-month long warranty commitment