Things to note when choosing bearing lubricant
Bearing lubricant analysis is crucial to maintaining normal operation of bearings. Its main functions are as follows:
- Reduce friction and wear: Lubricating oil generates an oil film on the bearing surface, reducing friction and wear between the bearing, the shaft and the bearing seat, thereby extending the bearing life.
- Prevent rust and corrosion: Lubricating oil can prevent the bearing surface from being eroded by water, gas and other substances, and avoid rust and damage problems.
- Give full play to heat dissipation efficiency: In high-speed or high-temperature environments, lubricating oil effectively takes away the heat generated by the bearing, reduces the operating temperature of the bearing, and improves its working performance and stability.
- Has a cleaning function: Lubricating oil helps clean dirt and impurities on the bearing surface, prevents them from invading the bearing structure, and protects its normal operation.
- It also has sealing and waterproof functions: The lubricating oil builds a sealing area between the bearings, blocking external clutter and moisture from entering, ensuring the bearing’s leak-proof and sealing performance.
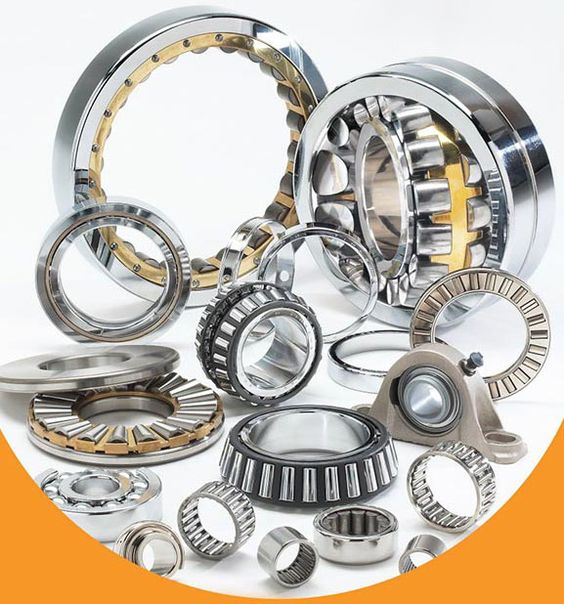
In order to ensure the normal operation of bearings, extend the overhaul cycle and improve work efficiency and reliability, it is crucial to select the appropriate lubricant. Based on the above functions, the following factors should be focused on when selecting lubricants:
- Suitable viscosity: The viscosity of lubricating oil has a direct impact on its fluidity and lubrication effect. The selection should be based on characteristics such as bearing pressure, speed and temperature, and should be maintained within a moderate range.
- Excellent oxidation stability: Bearing lubricating oil must have good oxygen resistance. Because it is easily oxidized by oxygen when left in the atmosphere for a long time, the performance of the lubricating oil will be damaged or even invalid. Therefore, lubricants with good antioxidant properties are preferred.
- Excellent anti-rust ability: The anti-rust properties of lubricating oil are related to the service life of the bearing. The added antioxidants can form a protective layer on the bearing surface to prevent it from being corroded, thus extending the bearing life.
- Excellent anti-foaming property: During the startup and operation of the machine, the lubricating oil will generate bubbles due to stirring. Such foam will weaken the lubrication effect and seriously shorten the bearing life. Therefore, it is crucial to choose a lubricant with good anti-foam properties.
- Good oil-water separation performance: In actual operation, lubricating oil will inevitably come into contact with water. If oil and water cannot be effectively separated, the lubricating oil will easily fail. Therefore, it is particularly necessary to choose lubricating oil with excellent oil-water separation ability.
In summary, when selecting bearing lubricants, multiple factors need to be weighed, such as appropriate viscosity, excellent antioxidant stability, excellent rust prevention capabilities, excellent anti-foaming properties, and excellent oil-water separation performance. In the process of selecting and using lubricants, it is necessary to fully combine the actual situation and comprehensively consider these factors in order to select the lubricant that best meets the requirements, so as to ensure the normal operation of the bearing and extend the service life.