what is a wheel bearing
The main function of the hub bearing is to bear the load and provide precise guidance for the rotation of the hub. It bears both axial load and radial load, and is a very important component.The wheel hub bearing unit is developed on the basis of standard angular contact ball bearings and tapered roller bearings. It integrates two sets of bearings into one. It has good assembly performance, can omit clearance adjustment, is light in weight, has a compact structure, and has a large load capacity. Large, sealed bearings can be filled with grease in advance, omit external hub seals, and are maintenance-free. They have been widely used in cars, and there is also a trend of gradually expanding their application in trucks.
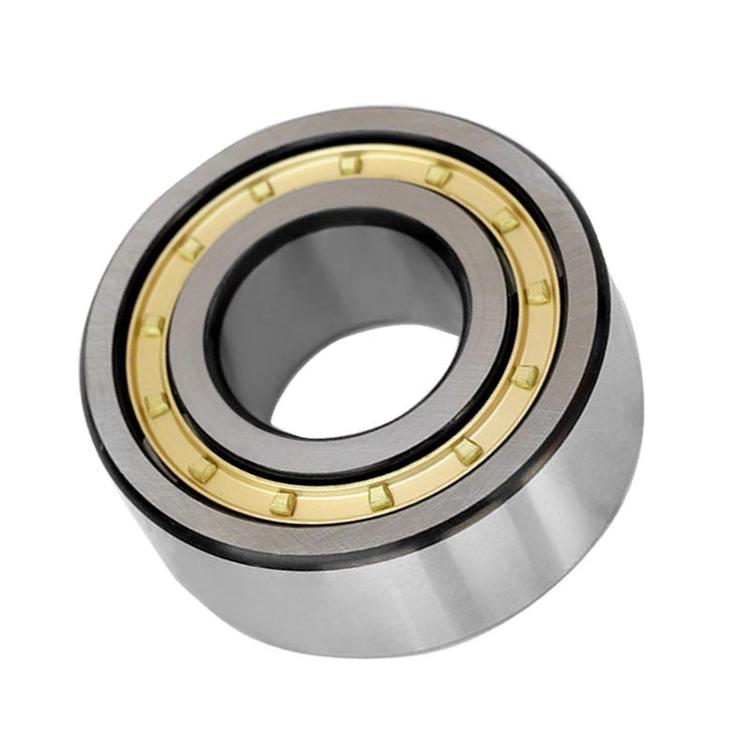
Installation and use of wheel bearings:
1.In order to ensure safety and reliability to the greatest extent, it is recommended that you check the hub bearings frequently no matter how old the vehicle is – pay attention to the early warning signs of bearing wear: including any friction noise during rotation or suspension combination wheels turning Abnormal deceleration. For rear-wheel drive vehicles, it is recommended that the front hub bearings be lubricated when the vehicle has driven to 38,000 kilometers. When replacing the brake system, check the bearings and replace the oil seal.
- If you hear the noise from the hub bearing, first of all, it is important to find the location where the noise occurs. There are lots of moving parts that could be generating noise, or some rotating parts making contact with non-rotating parts. If it is confirmed that the noise is in the bearings, the bearings may be damaged and need to be replaced.
- Because the working conditions of the front wheel hub causing bearing failure on both sides are similar, even if only one bearing is broken, it is recommended to replace it in pairs.
- Hub bearings are sensitive and in any case the correct method and suitable tools are required. In the process of storage, transportation and installation, the parts of the bearing must not be damaged. Some bearings require greater pressure to press in, so special tools are required. Be sure to refer to the vehicle manufacturer’s instructions.
- When installing the bearing, it should be in a clean and tidy environment. The entry of fine particles into the bearing will also shorten the service life of the bearing. It is very important to maintain a clean environment when replacing bearings. It is not allowed to hit the bearing with a hammer, and be careful not to drop the bearing on the ground (or similar mishandling). The condition of the shaft and housing should also be checked before installation, as even minor wear can lead to poor fit and premature failure of the bearing.
- For the hub bearing unit, do not attempt to disassemble the hub bearing or adjust the sealing ring of the hub unit, otherwise the sealing ring will be damaged and water or dust will enter. Even the raceways of the sealing ring and the inner ring are damaged, resulting in permanent failure of the bearing.
- There is a magnetic thrust ring in the sealing ring of the bearing equipped with the ABS device. This thrust ring cannot be subject to collision, impact or collision with other magnetic fields. Remove them from the box before installation and keep them away from magnetic fields such as those used by motors or power tools. When installing these bearings, change the operation of the bearings by observing the ABS alarm pin on the instrument panel through a road test