The ways to make bearings smooth
The purpose of bearing lubrication is to enable the bearing to operate normally, prevent direct contact between the raceway and the surface of the rotating body, reduce friction and wear inside the bearing, extend the service life of the bearing, enhance the performance of the bearing, and also prevent foreign matter from invading the interior of the bearing and causing Rust and degradation.
01 Manual smoothing
This is the original method. When the lubricating oil of the bearing is insufficient, an oiler is used to supply oil. However, this method is difficult to maintain a constant amount of oil, and there is a greater risk of forgetting to refuel. It is usually only used in situations of light load, low speed or intermittent movement. When operating, install a dust cover or ball valve on the refueling hole, and use Felt, cotton, wool, etc. are used as filter devices.
02 drops of smoothness
It is usually used for light-load and medium-load bearings whose peripheral speed is less than 4~5m/s. A roughly quantitative amount of lubricant oil is supplied from the container through holes, needles, valves, etc. The classic one is the dripping oil cup. The amount of oil dripping depends on the lubrication. There are significant changes in oil viscosity, bearing clearance and oil supply hole location.
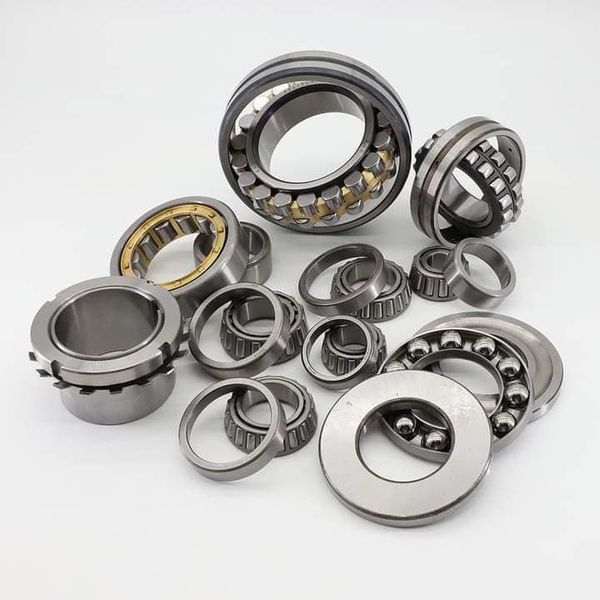
03 Oil ring is slippery
The lubricating oil from the oil pool is brought to the bearing by a ring that is hung on the shaft and can rotate (can only be used for horizontal shaft lubrication). It is suitable for medium-speed and high-speed bearings with a shaft diameter greater than 50mm. The oil ring is seamless , when the bearing width-to-diameter ratio is less than 2, only one oil ring can be used, otherwise two oil rings are required.
04 Oil rope is slippery
The capillary and siphon functions of the oil rope are used to guide the lubricating oil in the oil cup into the bearings. It is mainly used for light-load and medium-load bearings with a peripheral speed of less than 4 to 5 m/s. The rest of the oil rope can filter during the entire process. of dyeing.
05 Oil pad is smooth
Use the capillary diffusion of the oil pad to apply the lubricating oil in the oil pool to the surface of the shaft diameter. This method can keep the friction surface clean at all times, but dust will also suffocate the capillary pores and cause insufficient oil supply. The oil supply of oil pad lubrication is usually only 1/20 of that of oil lubrication.
06Oil lubrication
This lubrication method involves immersing part of the bearing in lubricating oil. It is often used for thrust bearings on vertical shafts, but not for radial bearings on horizontal shafts.
07 Oil tank lubrication
The lubricating oil splashed from the rotating parts in the oil tank is supplied to the bearings, which is suitable for bearings with higher speeds.
08 Spray lubrication
The lubrication method of atomizing lubricating oil and spraying it on the friction surface is suitable for high-speed bearings.