Luoyang Inno Bearing Co., Ltd.: Deep groove ball bearings help the development of new energy fields
Among many bearing companies, Luoyang Inno Bearing Co., Ltd. has always occupied a place in the market and served a large number of customers with its high-quality deep groove ball bearing products. Its products are widely used and have significant advantages.
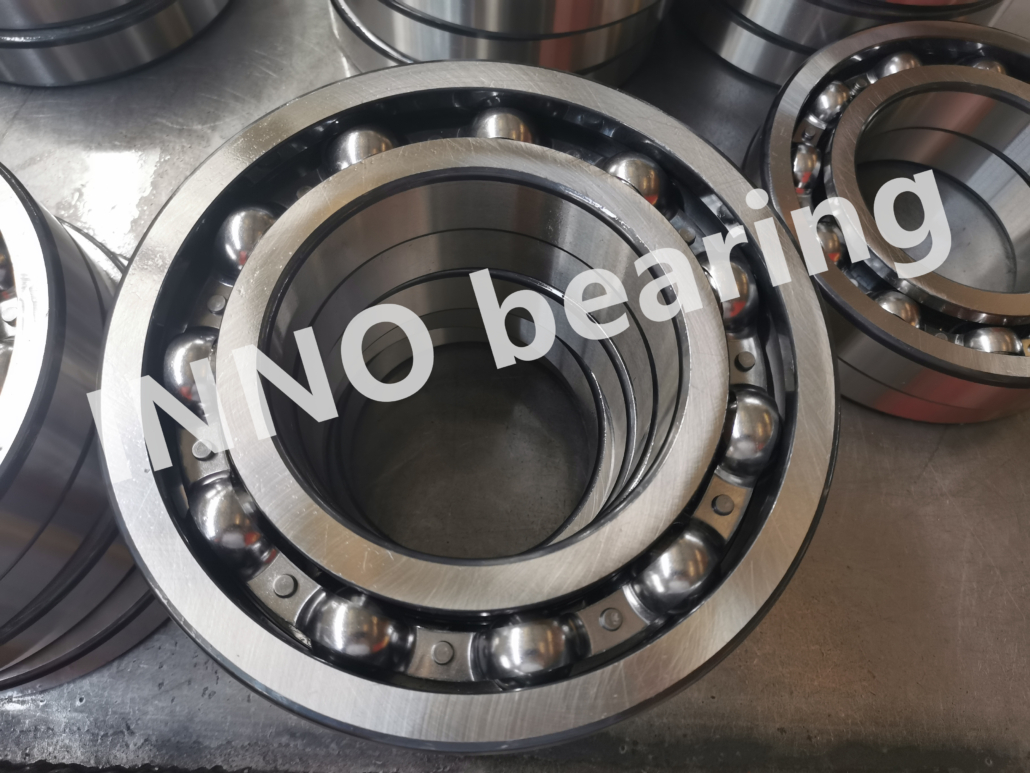
Deep groove ball bearings play a vital role in automated production lines and can ensure the precise operation of production lines. This feature greatly improves production efficiency and product quality, providing a solid guarantee for the development of the automation industry. At the same time, in the booming new energy vehicle field, deep groove ball bearings also show irreplaceable value. It is widely used in key components such as motors and transmissions, providing strong support for the development of new energy vehicles.
The company’s deep groove ball bearings have many advantages. It has good fatigue resistance and can maintain a stable state under long-term alternating loads, greatly reducing the probability of failure. In addition, it performs well in lubrication management, which can effectively reduce bearing wear and thus extend service life. It is worth mentioning that the company is very timely in product supply and can fully meet the urgent needs of customers. Even if customers have sudden order needs, they can respond quickly.
With the continuous development of the new energy vehicle industry, the requirements of new energy vehicle drive motors for bearings are becoming more and more stringent, especially in terms of speed and noise. The company’s deep groove ball bearings are a perfect match for these requirements. Deep groove ball bearings have the characteristics of low friction coefficient (0.001 – 0.005) and high limit speed, which can easily cope with the high speed working requirements of new energy vehicle drive motors.
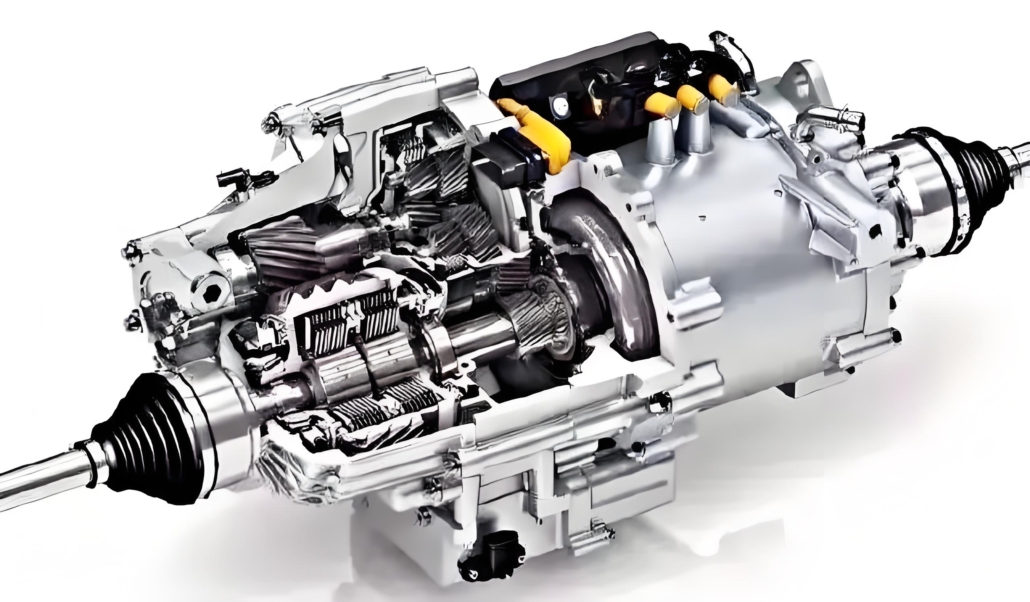
More importantly, Luoyang Inno Bearing Co., Ltd. actively develops and innovates, and has developed low-noise sealed bearings. The vibration value of this bearing is 15% lower than the national standard, and it performs well in noise control, creating a quiet and comfortable operating environment for new energy vehicles. At present, this low-noise sealed bearing has been used in batches in many new energy vehicle companies and has been widely recognized by the market. In the future, Luoyang Inno Bearing Co., Ltd. will continue to uphold the high-quality production concept, continue to innovate and make progress, and use high-quality deep groove ball bearing products to contribute to the development of more fields.